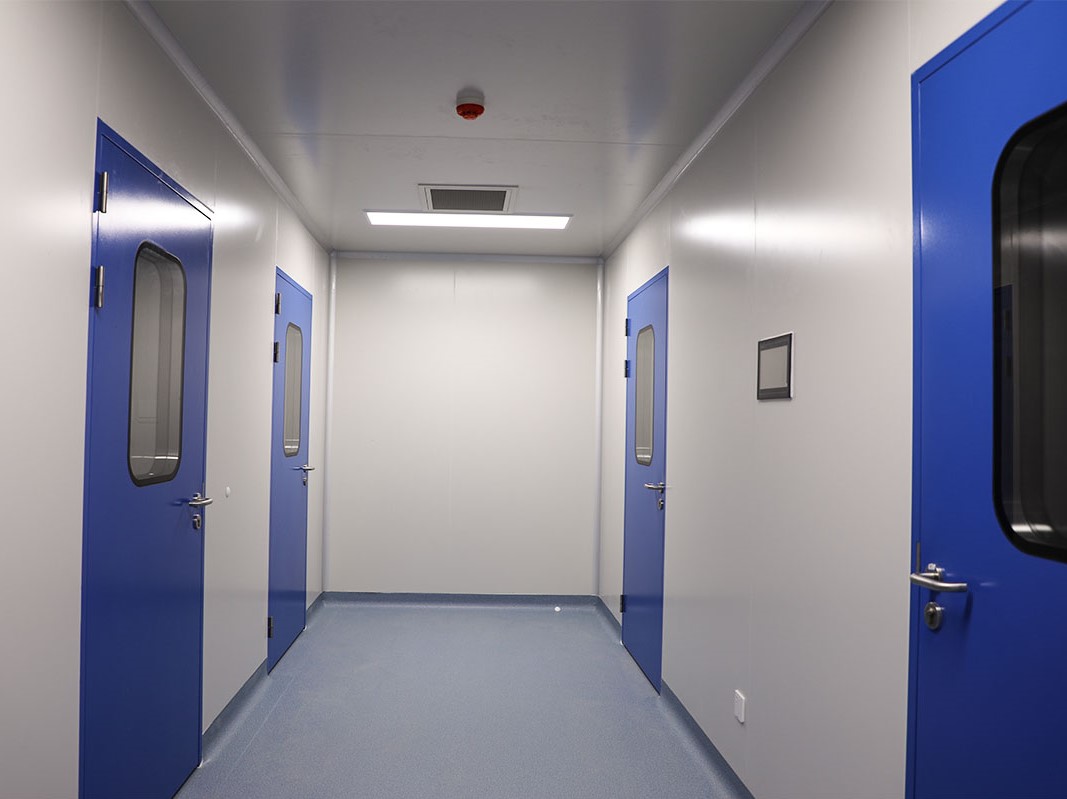
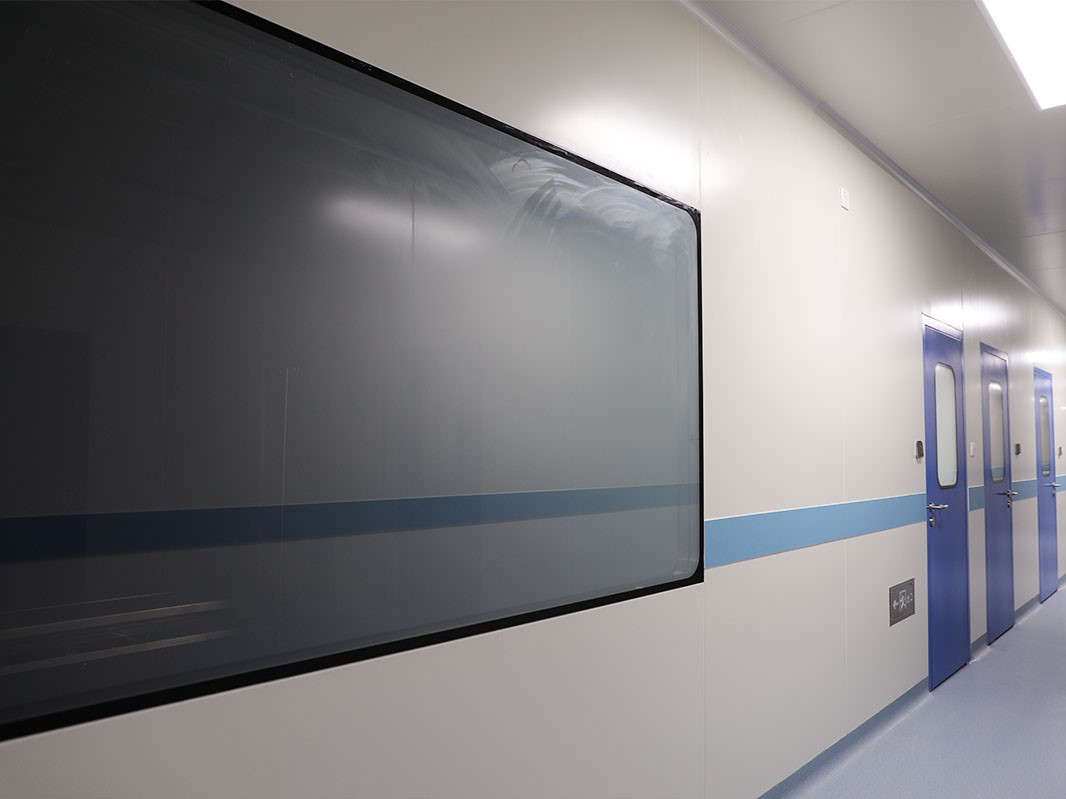
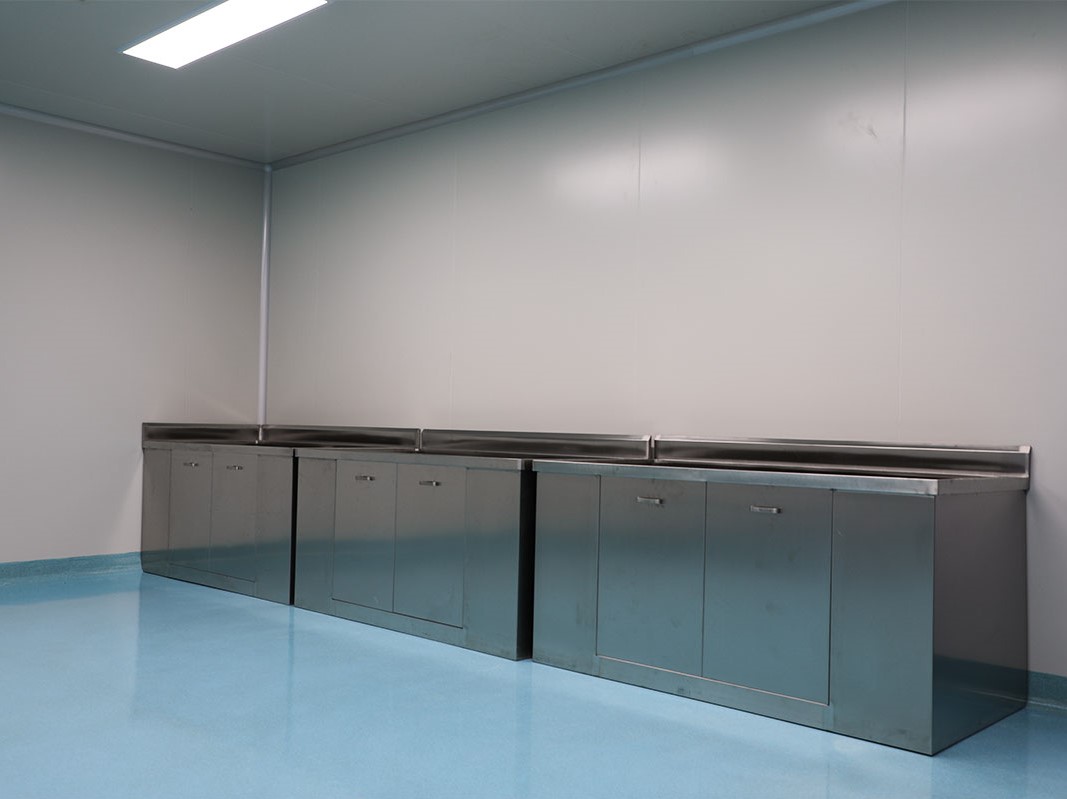
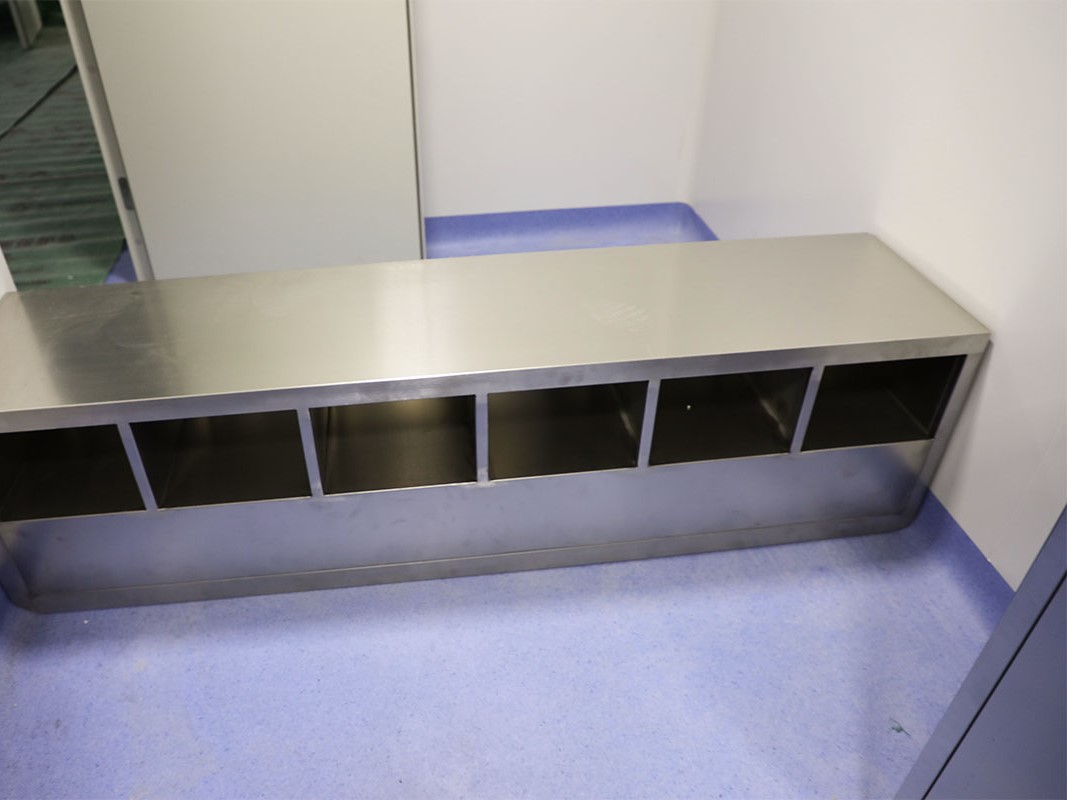
Seit seiner Veröffentlichung im Jahr 1992 wurde die "gute Herstellungspraxis für Arzneimittel" (GMP) in der chinesischen Pharmaindustrie nach und nach von Pharmazeutischen Produktionsunternehmen anerkannt, akzeptiert und umgesetzt. GMP ist eine nationale obligatorische Politik für Unternehmen, und Unternehmen, die die Anforderungen innerhalb der angegebenen Zeitlimit nicht erfüllen, werden die Produktion einstellen.
Der Kerninhalt der GMP -Zertifizierung ist die Qualitätsmanagementkontrolle der Arzneimittelproduktion. Der Inhalt kann in zwei Teile zusammengefasst werden: Softwareverwaltung und Hardwareeinrichtungen. Das saubere Raumgebäude ist eine der Hauptinvestitionskomponenten in Hardwareanlagen. Nach Abschluss des sauberen Raumgebäudes muss letztendlich durch Tests die Konstruktionsziele erreicht und die GMP -Anforderungen erfüllt werden.
Während der Inspektion des sauberen Raums scheiterten einige von ihnen die Sauberkeitsprüfung, einige waren lokal in der Fabrik und einige waren das gesamte Projekt. Wenn die Inspektion nicht qualifiziert ist, obwohl beide Parteien die Anforderungen durch Berichtigung, Debuggen, Reinigung usw. erreicht haben, verschwendet sie häufig viel Arbeitskräfte und materielle Ressourcen, verzögert die Bauzeit und verzögert den Prozess der GMP -Zertifizierung. Einige Gründe und Mängel können vor dem Testen vermieden werden. In unserer tatsächlichen Arbeit haben wir festgestellt, dass die Hauptgründe und Verbesserungsmaßnahmen für uneingeschränkte Sauberkeit und GMP -Misserfolg:
1. unangemessenes technisches Design
Dieses Phänomen ist relativ selten, hauptsächlich im Bau kleiner sauberer Räume mit geringen Sauberkeitsanforderungen. Die Konkurrenz in Clean Room Engineering ist jetzt relativ heftig, und einige Baueinheiten haben in ihren Angeboten, um das Projekt zu erhalten, niedrigere Angebote bereitgestellt. In der späteren Bauphase wurden einige Einheiten verwendet, um die Ecken zu schneiden und aufgrund ihres mangelnden Wissens, was zu einer nicht übereinstimmenden Versorgungsleistung und einem sauberen Bereich führte, was zu einer uneingeschränkten Sauberkeit führte, um eine nicht qualifizierte Sauberkeit zu erledigen. Ein weiterer Grund ist, dass der Benutzer nach dem Entwurf und dem Start des Designs und des Konstruktions neue Anforderungen und sauberen Bereiche hinzugefügt hat, wodurch das ursprüngliche Design die Anforderungen nicht erfüllen kann. Dieser angeborene Defekt ist schwierig zu verbessern und sollte während der technischen Entwurfsphase vermieden werden.
2. Ersetzen von High-End-Produkten durch Produkte mit niedrigem Ende
Bei der Anwendung von HEPA-Filtern in sauberen Räumen sieht das Land vor, dass für die Luftreinigungsbehandlung mit einer Sauberkeit von 100000 oder mehr eine dreistufige Filtration von Primär-, Medium- und HEPA-Filtern verwendet werden sollte. Während des Validierungsprozesses wurde festgestellt, dass ein großes Clean Room -Projekt einen Sub -HEPA -Luftfilter verwendete, um den HEPA -Luftfilter in einem Sauberkeit von 10000 zu ersetzen, was zu einer unqualifizierten Sauberkeit führte. Schließlich wurde der hocheffiziente Filter ersetzt, um die Anforderungen der GMP-Zertifizierung zu erfüllen.
3. Schlechte Versiegelung des Luftversorgungskanals oder -filters
Dieses Phänomen wird durch grobe Konstruktion verursacht, und während der Akzeptanz scheint es, dass ein bestimmter Raum oder ein Teil desselben Systems nicht qualifiziert ist. Die Verbesserungsmethode besteht darin, die Leckage-Testmethode für den Luftversorgungskanal zu verwenden, und der Filter verwendet einen Partikelzähler, um den Querschnitt, den Versiegelungskleber und den Installationsrahmen des Filters zu scannen, die Leckage zu identifizieren und sorgfältig abzudichten.
4. Schlechtes Design und Inbetriebnahme von Rückkehrluftkanälen oder Lüftungsöffnungen
In Bezug auf die Designgründe ist die Verwendung von "Top -Versorgungsseitenrendite" oder nicht genügend Rückgänge nicht möglich. Nach der Beseitigung von Entwurfsgründen ist das Debuggen von Rückkehrlüftungsöffnungen ebenfalls eine wichtige Bauverbindung. Wenn das Debuggen nicht gut ist, ist der Widerstand des Rücklaufluftauslasss zu hoch, und das Return -Luf -Volumen ist geringer als das Versorgungsluftvolumen, es wird auch eine uneingeschränkte Sauberkeit verursachen. Darüber hinaus wirkt sich die Höhe des Rückgangs aus dem Boden während des Baus auf die Sauberkeit aus.
5. Unzureichende Selbstreinigungszeit für das saubere Raumsystem während des Tests
Gemäß dem nationalen Standard müssen die Testbemühungen 30 Minuten nach dem normalen Betrieb der Reinigungsklimaanlage normal gestartet werden. Wenn die Laufzeit zu kurz ist, kann sie auch eine uneingeschränkte Sauberkeit verursachen. In diesem Fall reicht es aus, die Betriebszeit des Klimaanlagenreinigungssystems angemessen zu verlängern.
6. Die Reinigung der Klimaanlage wurde nicht gründlich gereinigt
Während des Bauprozesses wird das gesamte Klimaanlagensystem der Reinigung, insbesondere die Versorgungs- und Rückgabeluftkanäle, auf einmal abgeschlossen, und das Baupersonal und die Bauumgebung können die Belüftungskanäle und -filter zu Verschmutzungen führen. Wenn nicht gründlich gereinigt, wirkt sich die Testergebnisse direkt aus. Die Verbesserungsmaßnahme besteht darin, beim Bau zu reinigen, und nach dem vorherigen Abschnitt der Pipeline -Installation kann ein Kunststofffilm verwendet werden, um die durch Umweltfaktoren verursachte Verschmutzung zu vermeiden.
7. Workshop reinigen nicht gründlich gereinigt
Zweifellos muss ein sauberer Workshop gründlich gereinigt werden, bevor das Testen fortgesetzt werden kann. Erfordern Sie das endgültige Wischpersonal, um saubere Arbeitskleidung zum Reinigen zu tragen, um Kontaminationen zu beseitigen, die durch den menschlichen Körper des Reinigungspersonals verursacht werden. Reinigungsmittel können Leitungswasser, reines Wasser, organische Lösungsmittel, neutrale Reinigungsmittel usw. für diejenigen mit antistatischen Anforderungen sein, die mit einem in antistatischen Flüssigkeit getauchten Stoff gründlich abtauchen.
Postzeit: Jul-26-2023