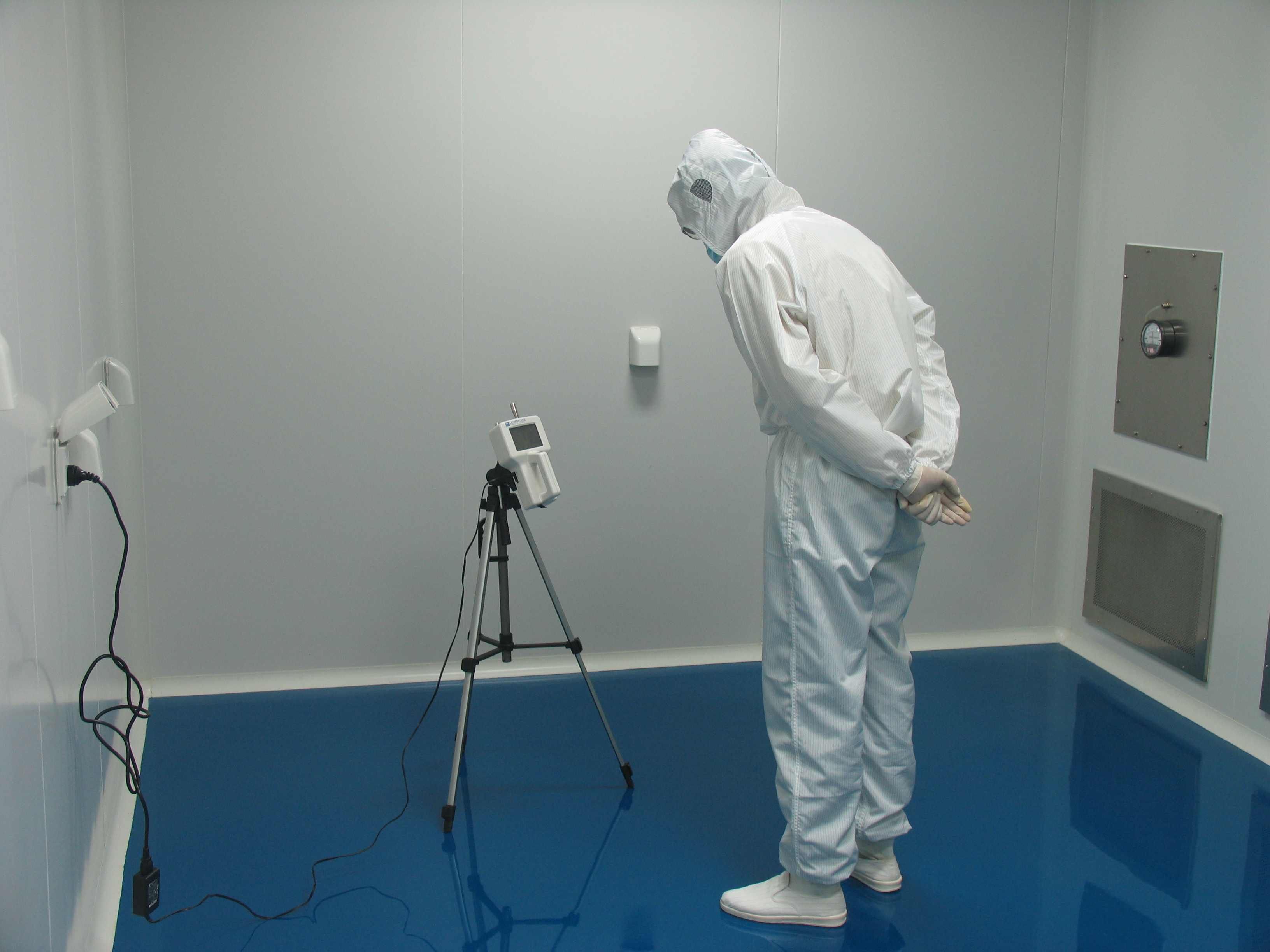
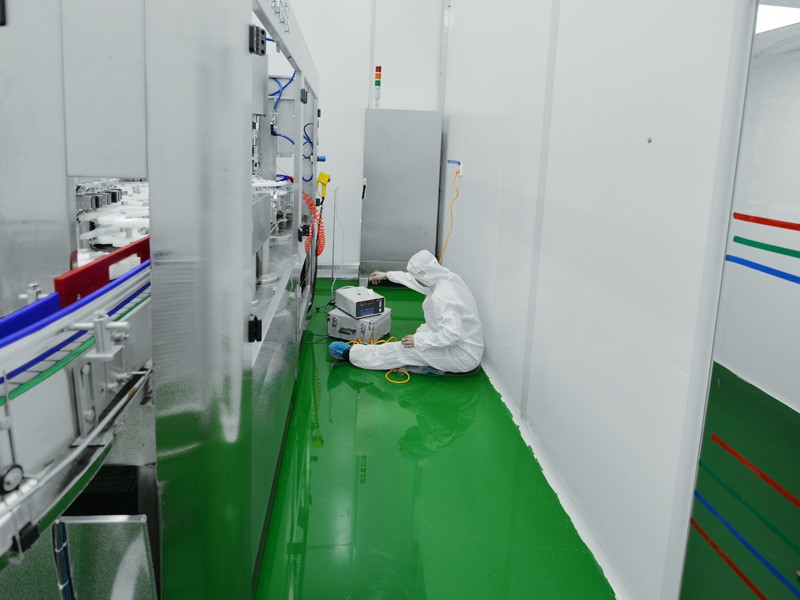
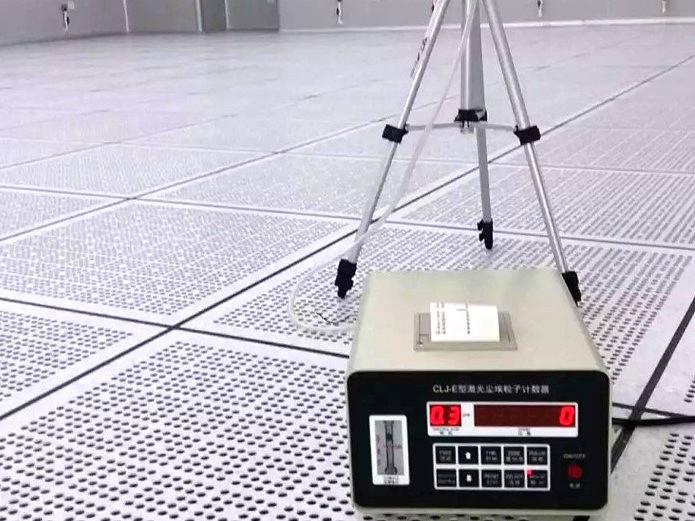
Um die GMP -Vorschriften zu erfüllen, müssen saubere Räume, die für die pharmazeutische Produktion verwendet werden, die entsprechenden Anforderungen an die Note erfüllen. Daher erfordern diese aseptischen Produktionsumgebungen eine strenge Überwachung, um die Kontrollierbarkeit des Produktionsprozesses sicherzustellen. Umgebungen, die eine Schlüsselüberwachung erfordern, installieren im Allgemeinen ein Satz von Staubpartikelnüberwachungssystemen, das: Steuerungsgrenzfläche, Steuerungsausrüstung, Partikelzähler, Luftrohr, Vakuumsystem und Software usw. umfassen.
In jedem Schlüsselbereich wird ein Laserstaub -Partikelzähler für die kontinuierliche Messung installiert, und jeder Bereich wird kontinuierlich überwacht und über den Befehl workstation computeranregungsbefehl bewertet, und die überwachten Daten werden an den Workstation -Computer übertragen, und der Computer kann einen Bericht anzeigen und ausstellen Nach Erhalt der Daten an den Bediener. Die Auswahl des Standorts und die Menge der dynamischen Online -Überwachung von Staubpartikeln sollte auf der Forschung der Risikobewertung beruhen, die alle Schlüsselbereiche abdeckt.
Die Bestimmung des Probenahmepunkts des Laserstaub -Partikeltischs bezieht sich auf die folgenden sechs Prinzipien:
1. ISO14644-1 Spezifikation: Für einen unidirektionalen Durchflussraum sollte der Probenahmeanschluss der Luftstromrichtung ausgesetzt sein. Für einen nicht unidirektionalen Durchflussräume sollte der Probenahmebericht nach oben und die Probenahmegeschwindigkeit am Probenahmeanschluss so nah wie möglich an der Luftstromgeschwindigkeit in Innenräumen sein.
2. GMP -Prinzip: Der Abtastkopf sollte in der Nähe der Arbeitshöhe und des Ortes installiert werden, an dem das Produkt freigelegt ist.
3. Die Probenahmebereich wirkt sich nicht auf den normalen Betrieb der Produktionsausrüstung aus und wirkt sich nicht auf den normalen Betrieb des Personals im Produktionsprozess aus, um zu vermeiden, dass der Logistikkanal beeinflusst wird.
4. Die Probenahmestelle verursacht keine großen Zählfehler aufgrund von Partikeln oder Tröpfchen, die vom Produkt selbst erzeugt werden, wodurch die Messdaten den Grenzwert überschreiten und den Partikelsensor nicht beschädigt werden.
5. Die Abtastposition wird über der horizontalen Ebene des Schlüsselpunkts ausgewählt, und der Abstand vom Schlüsselpunkt sollte 30 cm nicht überschreiten. Wenn in einer speziellen Position flüssiger Spritzer oder Überlauf vorhanden ist, was zu den Messdatenergebnissen führt, die den regionalen Standard dieses Niveaus unter simulierten Produktionsbedingungen überschreiten, kann der Abstand in vertikaler Richtung entspannend begrenzt sein, sollte jedoch 50 cm nicht überschreiten.
6. Versuchen Sie, die Probenahmeposition direkt über den Durchgang des Behälters zu platzieren, um nicht ausreichend Luft über dem Behälter und Turbulenz zu verursachen.
Nachdem alle Kandidatenpunkte unter den Bedingungen der simulierten Produktionsumgebung festgelegt wurden Punkte für Partikelabtastdatenprotokollierung.
Die Stichprobenergebnisse mehrerer Kandidatenpunkte im gleichen Bereich werden verglichen und analysiert, um den Hochrisiko-Überwachungspunkt zu ermitteln, um festzustellen, dass dieser Punkt eine geeignete Staubpartikelüberwachungspunkte der Probenahme-Kopf-Installationsposition ist.
Postzeit: Aug-09-2023